Toyota's Secret to Success: The Power of Human-Centric Production Systems
- David Frandsen
- 12 minutes ago
- 3 min read
The Toyota Production System (TPS) is indeed centered around people, despite being a production methodology. This human-centric approach is fundamental to TPS's success and effectiveness for several key reasons:
Respect for People
At the core of TPS is the principle of "Respect for People," which forms one of the two main pillars of the Toyota Way philosophy. This principle recognizes that employees are the company's most valuable asset and treats them accordingly. By valuing and respecting its workforce, Toyota creates an environment where employees feel motivated to contribute their best efforts and ideas.
Continuous Improvement (Kaizen)
TPS empowers employees at all levels to participate in the continuous improvement process:
1. Employee-Driven Innovation: Toyota encourages every employee to suggest improvements, implementing an average of nine ideas per employee per year. This approach taps into the collective intelligence and creativity of the entire workforce.
2. Quality Control Circles: Twice a month, assembly lines shut down for half an hour as employees gather in Quality Control Circles to study data and learn about their section and the company. This practice fosters a culture of learning and improvement.
3. Standardization and Improvement: Employees are encouraged to improve current processes, with successful ideas being standardized and documented by the innovator. This approach balances consistency with innovation.
Human Skills and Technology Integration
Toyota's approach combines human skills with innovative technology and digital tools. This integration recognizes that while technology is important, human judgment and creativity are irreplaceable in solving complex problems and driving innovation.
We have tried integrating human judgment with cutting-edge technology, creating a workplace that values both efficiency and creativity. This approach not only improves operational performance but also cultivates a motivated workforce capable of driving long-term innovation.
Leadership as Mentorship
In the TPS framework, leaders are expected to be mentors who actively engage with employees to understand their needs and guide their development. This approach fosters a supportive environment where employees can grow and develop their skills.
When mentors focus on transferring practical wisdom through real-world projects, cross-functional collaboration, and open dialogue, while emphasizing emotional intelligence and adaptability to bridge generational and cultural gaps. This fosters a culture where leaders engage in succession planning, ensuring organizational values and problem-solving technologies.
When we are prioritizing mentorship as a dynamic, two-way exchange a feedback loop exists and relationships often evolve into lifelong professional bonds. Our goal is to create leaders who drive innovation while maintaining the human-centric ethos at the heart of our operational excellence.
No-Blame Culture
TPS promotes a no-blame culture, focusing on process improvement rather than individual fault-finding. This approach encourages employees to report issues without fear, leading to more effective problem-solving and quality control.
Intrinsic Motivation
Rather than relying solely on financial incentives, TPS focuses on intrinsic motivation. Employees are driven by the desire to improve processes rather than by monetary rewards. This approach leads to more sustainable and meaningful engagement. I have found that implementing strategies that promote autonomy, mastery, purpose, and recognition, organizations can help employees find deeper meaning and satisfaction in their work, leading to improved performance and overall job satisfaction.
Autonomy and Trust
TPS gives frontline work teams the autonomy to set their own goals and improvement plans aligned with organizational priorities. This trust in employee expertise keeps team members highly motivated and empowered to drive change.
The people-centric approach of TPS is crucial because it:
1. Enhances problem-solving capabilities by leveraging diverse perspectives and experiences.
2. Improves employee engagement and job satisfaction, leading to higher retention rates.
3. Fosters a culture of continuous improvement that drives innovation and efficiency.
4. Builds a more resilient and adaptable organization capable of responding to challenges.
As we reflect on Toyota's remarkable success, it becomes clear that their approach offers a timeless lesson for any organization. By placing people at the heart of its production system, Toyota has created a methodology that not only improves efficiency and quality but also nurtures a workforce that is committed, innovative, and continuously striving for excellence. This is a lesson we can all learn whether we produce cars or managing public works. Ultimately, Toyota shows us that when we prioritize human ingenuity and empowerment, we unlock not just operational excellence but a culture of continuous improvement that benefits everyone involved.
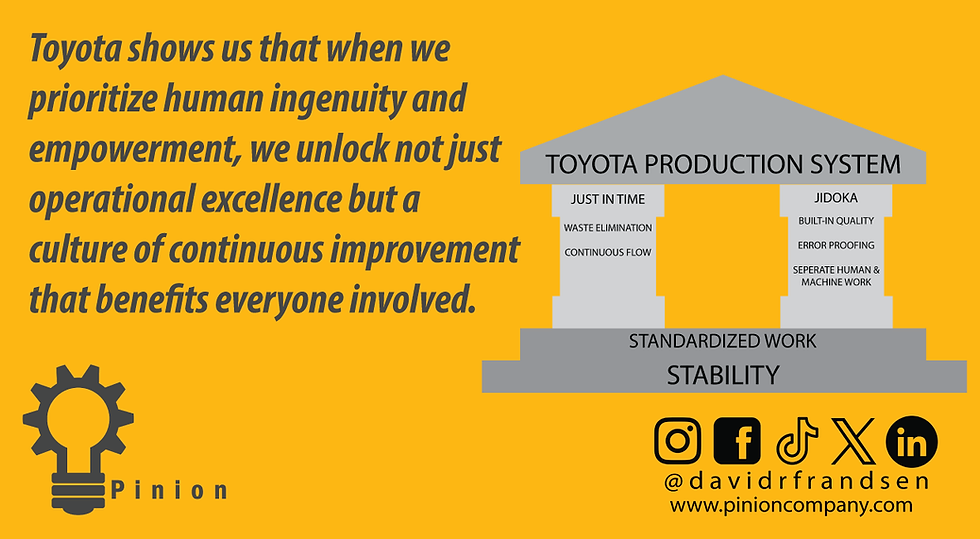
Comentários